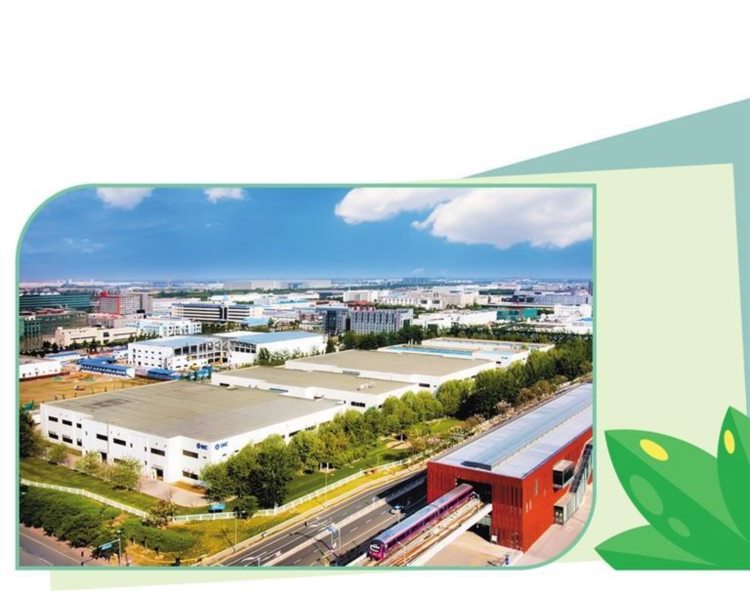
SMC(中国)有限公司第二工厂场景。(资料照片)
绿色制造是制造业转型发展的方向。2018年,我国首次制定并发布绿色工厂相关标准,按照“厂房集约化、原料无害化、生产洁净化、废物资源化、能源低碳化”原则,建立绿色工厂系统评价指标体系。2019年,SMC(中国)有限公司第二工厂被工信部授予“绿色工厂”称号。
走进位于北京经济技术开发区的SMC(中国)有限公司第二工厂,“简洁、流畅、洁净、高效”几个大字在车间白墙上格外醒目,这也是对生产现场直白的描述。在这个能完成4万多个品类部件加工的现代化工厂中,从原材料到成品,每个环节都有条不紊地运行着。
第二工厂于1996年建成,当时自动化还局限在单体设备上,需要人工上下料。“精密仪器制造对每个细节要求都很高,因此要让工厂运转更绿色、高效。”SMC投资管理有限公司总经理马清海告诉记者,公司专门组建了工艺创新团队,通过工业工程技术缩短生产周期,减少生产中能源消耗;通过信息技术全面优化业务流程,提高工作效率,推进精益化、数字化、低碳制造,力求将产品和生产过程对自然环境的影响降低到最小程度。
在第二工厂组装车间,一套全自动生产线是公司自动化和数字化改革成果的体现。这套自动化组装生产线通过接收自动排程系统发送的生产指示,自动切换生产所需参数并开始装配、生产,过程中物品取放、装配、检测、包装、移动、入库可全部实现自动化。
“顺应绿色制造大趋势,公司通过对既有工艺改造升级创新,标记每一项工艺的二氧化碳排放情况,减少能源使用。”马清海说,公司还使用流量传感器监控工厂的空气使用流量,在设备不运转时自动切断空气源的装置,使净化空气使用量减少30%。
在削减生产过程能耗的同时,公司着力开发低功耗的绿色产品,实现产品小型化、轻量化、节能化。
以气缸产品为例,以前,气缸生产需要的异型材需委托专业金属材料公司生产,成本很高。公司研发团队经过多年努力,攻克了异型材成型技术,实现型材挤压一次成型,达到精密加工的精度水平。目前,公司一年生产约1万吨异型材,进一步降低气缸成本,带来丰厚收益。
“通过优化设计,在与以前产品缸径、行程相同的条件下,紧凑型气缸实现省空间、轻量化,大幅减少制造过程中的二氧化碳排放量。同样性能的气缸制造高压气的使用量是旧产品的50%。”马清海说。
公司还将绿色制造的触角延伸到合作伙伴身边,通过调查与诊断,为客户提供设备节能改善的建议,帮助客户实现生产应用中的节能。比如,工厂约20%耗电量是气动设备消耗的,其中吹气系统的空气消耗量占气动系统能耗的40%以上,可以通过优化设备来提高吹扫效率。公司组建了约30人的节能团队,每年帮客户减排约1万吨二氧化碳。
“顺应国家‘双碳’目标,我们未来建设的新工厂将采用更多数字化手段,让工厂对人的依赖更小、柔性化程度更高。”马清海说。(本报记者 杨学聪)