来源:【铁人先锋】
十年磨一剑,终成大器。
广东揭阳,南海之滨。在这片热土上,一座绿色、智能、效益型世界级炼化一体化基地拔地而起。
向大洋,碧海潮涌;向内陆,市场广阔。充分利用“两种资源”“两个市场”,及大湾区炼化产业集群星状辐射的优势,广东石化项目如南海春潮般,焕发着前所未有的生机与活力。
矗立起的,不只是一座座炼化装置,更是我国石化工业加快奔向世界一流、打造石化强国路上的一座里程碑。
这是大力实施创新驱动发展战略,实现高水平科技自立自强,建设国家战略科技力量和能源与化工创新高地的铿锵步伐。
这是全面推进数字化转型、智能化发展,打造智能炼化工厂的样板工程。
这是践行“双碳”战略,坚持生态优先理念,发展绿色石化产业的长远之路。
这是推动世界一流企业建设,强化从严管理、精细管理、精益管理的宝贵实践。
一项项创新超越,一个个纪录突破,多个“之最”“第一”是汗水的浇筑,也是实力的铸造。
建设能源强国,托举大国重器,这颗闪耀的“石化明珠”必将在新征程上续写新传奇。
创新引领
建设世界级石化基地,创新是关键。从源头设计到开工建设再到全面投产,广东石化大力实施创新驱动发展战略,在建设国家战略科技力量和能源与化工创新高地上迈出了新步伐。
广东石化的创新,从它的“灵活”“任性”就可见一斑。炼油、化工装置协同优化,使得广东石化项目不仅规模大,而且可根据市场变化灵活调整生产。项目以多地劣质重油作为原料,通过优化技术路线生产出优质的石油产品和化工原料。“吃粗粮,产精品”,且实现了“宜油则油、宜芳则芳、宜烯则烯”,灵活的产品结构设置,是全球加工劣质重油领域的有益探索。
广东石化的创新,可以从它的“骨气”“争气”讲起。建设世界级项目,意味着要面对诸多世界级难题。广东石化加工的原料,包含世界上最难加工的Merey16劣质重油,项目炼油区装置均应用了先进成熟的技术,可满足装置的长周期稳定运行要求。在60万吨/年烷基化项目中,石化院自主开发新型催化剂,成功解决烷基化装置原料选择加氢核心问题,填补了国内技术空白。广东石化在建设中广泛运用自有技术和国产化装备,特别是120万吨/年乙烯装置,应用了全国最大的液体裂解炉,“三机组”为乙烯安上“中国心”,采用自有技术、自主管理、自主设计、自主采购、自主施工的全套乙烯装置,对于提升核心竞争力、走向国际有着重要意义。
广东石化的创新,体现在一项项“第一”和“首创”上。重大工程,需要一个个“之最”来支撑。广东石化在建设过程中,创新探索出符合企业实际的炼化一体化技术路线,也创造了5项“之最”:国内最大常减压电脱盐、国内最大气分装置、全球单套最大对二甲苯装置、全球单线能力最大聚丙烯装置、全球单套最大苯乙烯装置,主要技术经济指标都达到世界一流水平。
数智赋能
数字化转型升级是现代石油和化工企业实现高质量发展的必然趋势。从广东石化项目诞生的那一刻起,数智基因就镌刻在项目的“DNA”里。
面对技术发展日新月异的形势,广东石化紧盯新领域、新赛道、新动能、新优势,敢于超越,不断突破,让数字化、智能化——这个“最强大脑”在世界级石化基地中发挥出巨大作用。
“最强大脑”树立标杆争当示范。打造中国石油炼化一体化全流程智能工厂样板工程,是广东石化奋进的目标。作为新型炼厂,在总体设计时,广东石化以具有前瞻性的新一代智能工厂架构,绘制了符合国际数字化、智能化发展趋势的技术路线图;在建设过程中,广东石化充分采用新技术,应用新架构、新平台,研发新软件、新模型、新算法,不断夯实智能“底气”。这些极强的后发优势让广东石化智能工厂成为中国石油第一个实现同步规划设计、同步建设、同步投入使用的项目,也成为数字化转型、智能化发展上的行业标杆。
“最强大脑”赋能全厂智能升级。在广东石化公司和昆仑数智公司的紧密协作下,项目量身打造了34套智能化系统,直接参与从生产运营到财务运转的方方面面。在看不见的空间里,这些系统无处不在:炼油与化工运行系统让管理和调度身临生产现场;生产协同优化系统为装置试车提供最优调度方案;储运物流自动化系统让物流精准快速流动……广东石化通过工业互联网、云计算、数据集成等先进技术为数字化转型赋能,做到本质安全、绿色环保、合规管理,实现了智能工厂建设目标。
“最强大脑”助力实现实时管控。在施工建设期间,广东石化基于三维数字化工厂开展“三查四定”问题管理、全厂多介质管线抽离等应用,改变了传统工作模式,大大提高了工作效率。在生产运营期间,针对试生产初期操作不平稳、自控投用率低等情况,广东石化运用全流程智能控制系统的Robust-M智能建模等技术,实现了装置智能化控制。此外,全厂1万多台(套)设备能够进行全生命周期管理,在实现数据在线预览和智能分析的同时,确保设备故障源头可溯、责任可追。
绿色先行
走进广东石化项目现场,整齐划一的巨大储罐、纵横交错的管廊矗立在蓝天白云下。更远处,阳光照射在海面上,随手一拍都是美景。
绿,已成为广东石化项目从始至终的追求。从源头设计到建设管理,从清洁生产到产品性能,广东石化围绕“绿”擘画蓝图并付诸实践,走出一条生态优先、绿色发展的新路子。
绿,体现在源头设计上。广东石化将“绿色”确定为建成世界级石化基地的首要目标,不仅环保投资占总投资的11%以上,高于国内同类型项目,而且执行国内最高环保标准,从“生产工艺清洁化、资源利用高效化、产品结构最优化、节能减排最大化、污染防治系统化、环境监管智能化”六个方面入手,显著提升项目污染防治、环境监控、节能降耗和清洁生产水平。
绿,体现在建设管理上。广东石化积极探索绿色发展路径。一方面,坚持强化环境管理与监测,设立环境空气质量自动监测站,实施立体化、全天候的动态监控;另一方面,注重建设现场环境保护,建立健全生态补偿机制,相继完成2期1690万尾鱼虾苗增殖放流工作,为地方生态的可持续发展作出积极贡献。
绿,体现在清洁生产上。广东石化积极统筹“发展”与“减碳”关系,立足构建绿色化工产业,打出一套“组合拳”——在废气、废水、废渣和噪声及地下水污染治理方面,参考京津冀、珠三角地区特别排放限值要求,二氧化硫、氮氧化物、颗粒物、氨氮等污染物排放系数均低于同规模项目。在提高资源利用率方面,积极促进污水、余热资源的循环利用,在炼化生产装置及罐区建立全覆盖的污水预处理设施,污水处理场是中国石油首套采用PACT+WAR工艺处理高含盐污水的污水场。此外,按照“以汽定电”的原则确定动力中心规模,实现能量梯级利用,并充分回收利用全厂余热,为项目减少能源消耗。
绿,体现在产品性能上。广东石化项目投产后将主打绿色环保产品,所产汽柴油产品全部达到国Ⅵ标准,为国民经济发展提供可靠绿色的能源保障。同时,广东石化将加大在化工新材料方面的开发力度,逐绿前行,继续绘就发展最美底色。
管理现代
使用的混凝土能浇筑22个鸟巢,钢结构能搭建41个水立方,管线能从广州铺到哈尔滨,建设高峰期有100多家企业4万名员工……
从蓝图变杰作,广东石化不仅要面对项目规模大、投资大、管理界面复杂等必然挑战,还要应对多变的天气、反复的疫情等不确定因素。在这样的背景下,如何组织好、管理好这一“巨无霸”项目,考验着管理者和建设者的能力和智慧。
“一盘棋”统筹,合力建成超级工程。广东石化公司以目标为导向,优化企业管理,不断推动公司治理体系和治理能力现代化。项目在集团公司党组的坚强领导下,总部部门和专业公司协同管理,上下游整体联动,统一部署、分工合作,充分体现了专业化发展、市场化运作、精益化管理、一体化统筹的“四化”治企准则。
“一体化”管理模式,发挥协同作战优势。从开工建设到投产,广东石化公司和各参建单位艰苦奋战、众志成城,采用先进的“业主+PMC+EPC”一体化项目管理模式,助力项目跑出“加速度”、赛出“新高度”。在广东石化公司的召集下,各方力量齐聚公司会议室是数年间的常态。大家纷纷汇报各自工作进展,共同研究解决制约项目推进的问题。2020年至2022年,累计召开150多次周调度会、100多次工程协调会。一次次会议的成功举行、各方力量的有机融合,离不开“业主+PMC+EPC”项目管理模式的加持——这个模式充分发挥了业主、总包、施工单位、专业管理团队、监理等单位协同作战的优势,全面落实主体责任、直线责任、专业责任和属地责任,促进了项目的一体化推进。
“强管理”贯穿始终,确保项目高质高效。从设计阶段开始,广东石化公司就对标国际先进炼化企业,创新企业组织管理模式,提高生产效率,实现少人高效。同时,树牢“从严管理出效益,精细管理出大效益,精益管理出更大效益”理念,并将“强管理”贯穿于施工收尾、生产准备、投料试车工作中。在全面试产阶段,公司不断加大专业化管理力度,加强对生产波动、平稳操作率等指标的严格管控,持续在长周期运行、生产组织优化、产品结构优化等方面精耕细作,确保项目平稳运行。
亮点聚焦
作为中国石油炼化业务转型升级的战略工程及推动粤港澳大湾区地区经济发展的重点工程,从开工建设到投产,广东石化炼化一体化项目捷报频传,创下了众多国内、亚洲乃至世界纪录。
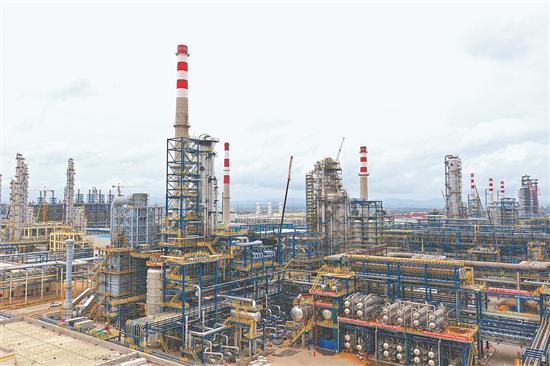
常减压装置I的电脱盐罐为国内最大电脱盐单体设备。两套年1000万吨常减压装置,将合力为广东石化提供2000万吨/年的原油处理能力。
120万吨/年
120万吨/年航煤加氢装置为国内操作压力最高的航煤加氢装置。
6.86万个
三聚立体仓库拥有6.86万个货位,可存储10.329万吨三聚固体料,为国内最大、自动化程度最高。
220℃
设计建造了满足220℃高温的渣油存储罐,属国内首次。
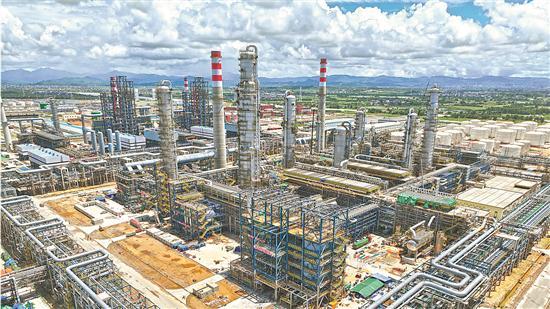
260万吨/年对二甲苯装置,为目前全球单套生产能力最大的对二甲苯装置。
78万吨/年
78万吨/年硫黄回收装置为国内总规模最大的硫黄回收装置。
370万吨/年
370万吨/年加氢裂化装置为中国石油系统内唯一采用两段转化工艺的加氢裂化装置。
4606吨
使用世界最大的5000吨门式起重机和4000吨履带起重机联手整体吊装4606吨的抽余液塔,刷新亚洲最重石化塔器吊装纪录,被誉为“亚洲第一吊”。
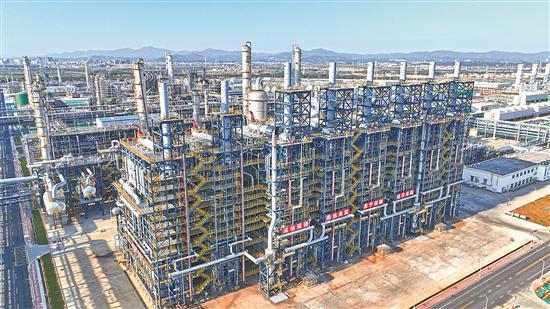
120万吨/年乙烯装置,采用寰球公司工艺包,为目前国内最大规模的国产乙烯工艺包。
110万吨/年
110万吨/年气分装置为国内最大规模。
40万吨/年
40万吨/年高密度聚乙烯装置为国内单线最大混配料(本色料、黑料)生产装置,投产后可进行黑料生产,扭转国内市场过分依赖进口产品的被动局面。
330万吨/年
柴油加氢裂化装置是国内目前单套处理能力最大的柴油加氢裂化装置,年加工能力达到330万吨。
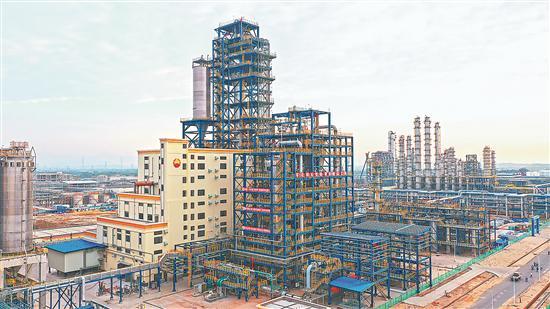
50万吨/年聚丙烯装置,为目前全球单线能力最大的聚丙烯装置。
100%
石油焦制氢装置是全国首套采用百分百石油焦制氢气的联合装置。
80万吨/年
80万吨/年苯乙烯装置是全球单套规模最大的苯乙烯装置。
橇块安装
在蜡油加氢处理装置施工中,开创中国石油首个方炉整体橇块安装先河。
本文来自【铁人先锋】,仅代表作者观点。全国党媒信息公共平台提供信息发布传播服务。
ID:jrtt