
记者 | 阮希琼
图片来源 | 受访者提供
在一条条生产线上,产品的原材料收货、进库、上料、生产、成品发运全部实现自动化;在一块块屏幕前,可以监控并分析每一个工位的生产情况,甚至可以洞悉分布在不同国家、100多家工厂的流水线运行情况……走进延锋座椅临港工厂,你就能切身体会到智能制造的科技魅力。
事实上,延锋座椅临港工厂只是华域汽车诸多数字化工厂中的一家。根据规划,2022-2023年,华域汽车将完成“新建10家数字化工厂,并在沪外复制10家数字化工厂”的阶段性目标,循序快进地推进数字化工厂建设。不仅如此,记者在华域汽车2022年度数字化制造推进工作会议上获悉,今年,华域汽车要在建设数字化工厂的基础上,进一步向数字化管理的“深水区”挺进。


三大梯队
数字化工厂建设循序快进
2020年,华域汽车以标杆先行、重点突破的方式,开启了智能制造转型工作。过去两年,延锋内饰金桥工厂等两家获得国家智能制造试点示范工厂称号,纳铁福康桥工厂等十家被评为上海市百家智能制造工厂。而这两年是华域汽车分级分类、复制推广数字化工厂的关键时期。
“为了有序地推进数字化工厂的建设工作,我们将企业分成了三大梯队。”华域汽车副总经理许林华说,“第一梯队是华域的头部企业,目标探索更多智能制造新技术的应用,将数字化推广至全国各地,甚至是世界各地的工厂,并向供应链延伸;第二梯队是华域的中坚企业,目标充分利用第一梯队的推进经验,从总体战略规划出发,打造数字化工厂。”
数据显示,华域汽车旗下各企业工厂的自动化水平已大幅提高:从2019年到2022年,AGV(自动导引运输车)的数量增长了91%;机器人的数量增长了26%;数据采集数增长了19%。

延锋座椅临港工厂的座椅后排骨架自动上线项目、博世华域的人机协作自动化项目、制动系统上海工厂的卡钳装配柔性线自动化改造项目……2022年,在数字化工厂的推广过程中,华域汽车共立项数字化项目180多个。
不仅如此,华域智能制造知识共享平台也随之建立起来。如今,该共享平台已积累了165个案例、158位智能制造相关人才,以及140个相关资源。“兄弟企业的推广经验具有很好的借鉴意义。”一名企业负责人表示。
在华域汽车的规划中,随着分级分类、复制推广工作的不断推进以及《华域汽车数字化工厂评价体系》的不断完善,到2025年,华域旗下将有超过70%的工厂成为数字化工厂。

标杆先行
迈向管理数字化“深水区”
“资源的配置和管理,原来大多依赖人的经验去做决策,现在将由数据说了算。”工厂里,一名工作人员告诉记者。
当数据被收集、管理和分析,就如同一个个活起来的“管理人员”,有的甚至像人类同事一样,拥有工号,成为了“数字员工”,在华域汽车各家工厂和企业承担起了人力管理、订单管理、流程管理、预算管理等工作。
这些“数字员工”可以通过预算与精细化制造、供应链、质量等费用的联动,使得预算更加全面、精细、准确;可以根据原材料的库存、装配计划和完成的数据,智能预测物料需求;可以胜过“老法师”,基于视觉和影像等感知技术在现场检测产品制造质量。
在某种意义上,酷炫的机械臂只是数字化转型“看得见的手”,而真正嵌入经营管理各流程的那些“看不见的手”,才是企业数字化转型真正的核心能力。对于华域汽车而言,工厂数字化是基础,下一步便是迈向管理数字化“深水区”。“这也是今年华域智能制造头部企业的重点工作。”许林华表示。
在今年各企业的分享环节,我们看到了更多关于管理数字化的优秀案例。比如,为适应数字化转型和新的竞争环境而在企业试点开展的基于数字化技术的管理流程重构;比如,构建管理驾驶舱,在这个驾驶舱内,管理人员可以看到工厂各层级的指标数据,工厂全局透明可视,同时提供分析服务,助力企业实现区域化协同、各地工厂的快速纳管;再如,建设碳管理系统,开展碳排放监测和工厂碳足迹追溯,形成准确可靠、透明可追溯的碳排放数据资产,实现全球工厂的碳排放监测与管理,支撑产品碳足迹分析和组织碳披露……
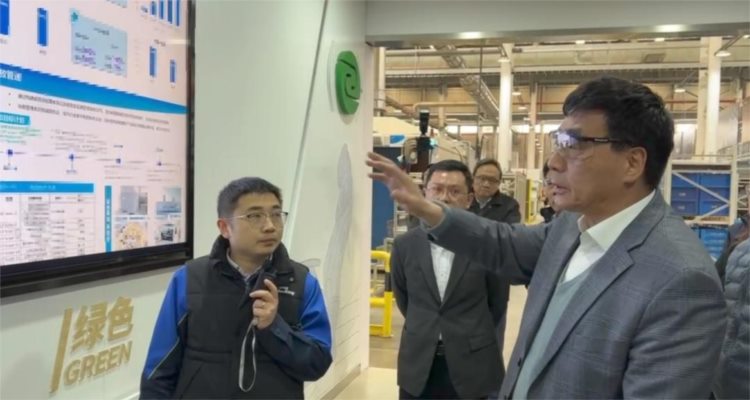
“如今的汽车工业有着太多的不确定性。华域汽车如何在当前这个不确定的环境中,缩小模糊的边界,使我们的工作更具有确定性,沿着正确的方向前行,始终是我们思考的问题。”会议最后,华域汽车总经理张海涛指出,“这也对我们企业管理者的判断能力、应对能力、前瞻性能力提出了极大的挑战。而只有当这三个能力都建立在管理体系上,并以数字化作为基本平台,才能提升对模糊边界的判断力,快速响应,使得决策更加准确。”
过去完全依赖经验来进行管理的时代已经结束。“如果不把数字化平台打造起来,想要成功几乎不可能。”张海涛直言。同时,他指出,对于开展管理数字化,各企业要进一步梳理好业务流程和管理体系,细化管理颗粒度,推进精细化管理,提升管理效率。