上海航天精密机械研究所航天离散制造智能工厂
智能制造是我国加快建设制造强国的主攻方向,是上海城市数字化转型的重要抓手。智能工厂是推动智能制造的切入点和突破口,是制造业数字化转型的重要载体,以智能工厂为载体布局新赛道、触发新动能、带动新终端,从而实现制造业高质量发展。
为统筹全市智能制造高质量发展,市经济信息化委联合9个委办局发布《上海市推进智能工厂建设 领航产业高质量发展行动计划(2022-2025)》。全市将按照“强引导、立标杆、树典型、广覆盖”的原则,“增量+提质”双轮驱动,全面实施智能工厂领航行动(简称“20035”工程)。通过打造20家标杆性智能工厂、建设200家示范性智能工厂和带动新增20000台工业机器人应用,实现3个全覆盖和5个倍增。一是聚焦六大重点产业,实现三个全覆盖。规上工业重点企业实现智能制造评估诊断全覆盖,重点区域(五个新城和南北转型区)规上工业重点企业实现数字化网络化全覆盖,六大重点产业链主企业实现智能化全覆盖。二是锚定高质量发展目标,实现五个倍增。五个智能制造核心指标实现倍增(简称:SMART):即智能制造标准制修订数(S-Standard)、智能制造装备产业规模(M-Manufacture),应用场景推广数(A-App),工业机器人产量(R-Robot), 智能制造新技术突破数(T-Technology)。
下一步,上海将围绕智能工厂领航行动,多措并举、持续发力,分级分类推进智能工厂梯度建设,促进实体经济智能制造转型升级。
2020年-2022年市经济信息化委认定授牌了100家上海市智能工厂,主要聚焦在汽车、电子信息、高端装备、生命健康、先进材料、时尚消费品等6个产业领域。为了总结和分享智能工厂建设经验,遵循“树典型、强引导、立标杆”的原则,我们分领域、分批次对100家智能工厂进行详细报道。
项目简介
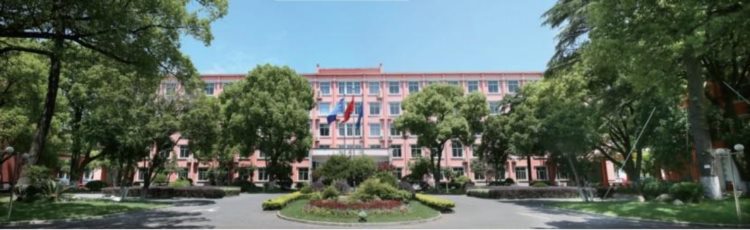
上海航天精密机械研究所航天离散制造智能工厂位于上海松江,工厂以自主研发的航天离散协同制造工业互联网赋能平台为基础底座,结合智能传感与控制、机器人、人工智能和数字孪生等新一代ICT技术,对标“黑灯工厂”,建成了具备设计制造一体化、设备互联智能化、仓储物流数字化、生产管控透明化功能的智能工厂,大幅提升了航天产品数字化研制批产能力,走出了航天“老厂换新”的独特模式。
项目亮点
航天离散制造智能工厂围绕航天产品研制全周期数字主线,挖掘智能工厂“数据-知识-模型”演进规律,建立了“工厂-车间-产线/单元-设备”分层管控体系。
数字化赋能平台:“平台+APP”保障业务场景快速落地
航天离散制造智能工厂通过开展新型航天离散协同制造工业互联网关键技术研究,研发了面向军工企业、离散制造行业的新型数字化转型基础设施,按照“平台+APP”方式,打造了面向离散制造行业企业级的工业互联网平台,开发了面向业务需求的数据挖掘和AI算法库与机理模型,面向业务需求快速构建解决业务痛点的工业场景,赋能企业数字化转型升级。
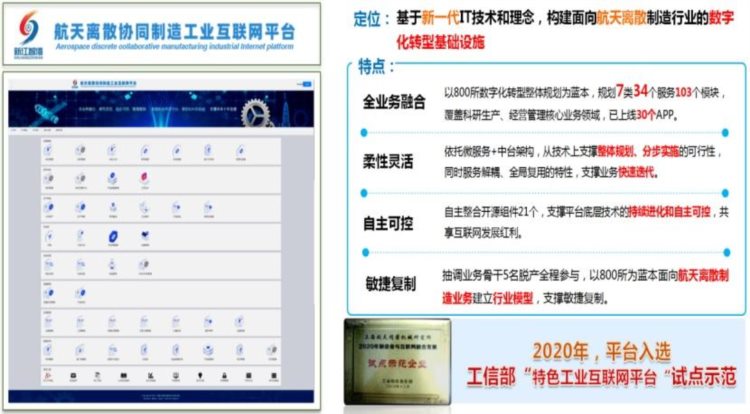
工艺数字化设计:模型驱动助力加工工艺高效设计
针对航天产品多品种、变批量、短周期、高可靠性的生产特点,以及航天型号复杂结构件研制“二维为主、三维为辅”的数字化制造模式下存在的设计制造环节自动化程度低、人工干预多,且存在大量重复性工作问题,开展模型驱动的定制产品智能工艺设计技术研究,研发了智能编程工具软件,实现了基于MBD三维模型一键式生成数控加工程序,从而降低复杂结构件数控加工工艺准备过程的重复性工作量与人工干预,实现数控加工工艺规划与编程效率的显著提升。
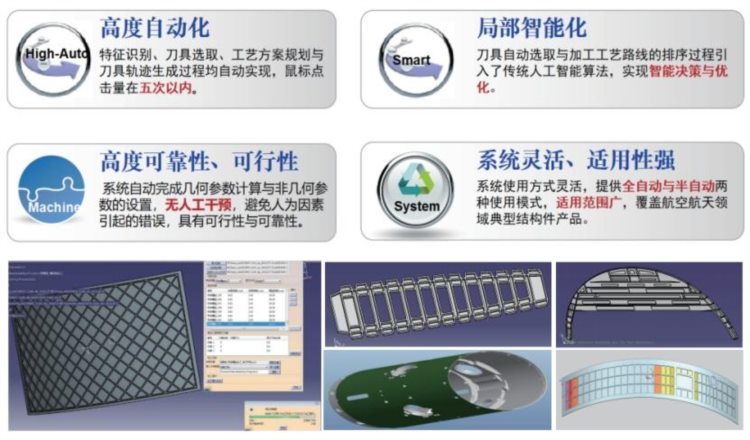
智能排产与调度:高效寻优算法提高资源快速优化配置水平
航天离散制造智能工厂通过研究航天制造分层(设备-单元\产线-车间)跨域(机料法控)的协同作业关系,通过NP(Nested Partition,嵌套分割)理论框架,研究智能排产高效寻优算法,通过“数据-模型-反馈”的功能链路,解决航天产品生产过程资源配置机理模型不清、多扰动情境下排产手段匮乏、快速动态调度工具不足等问题,有效提升了车间异常敏捷高效处理和资源快速优化配置水平。
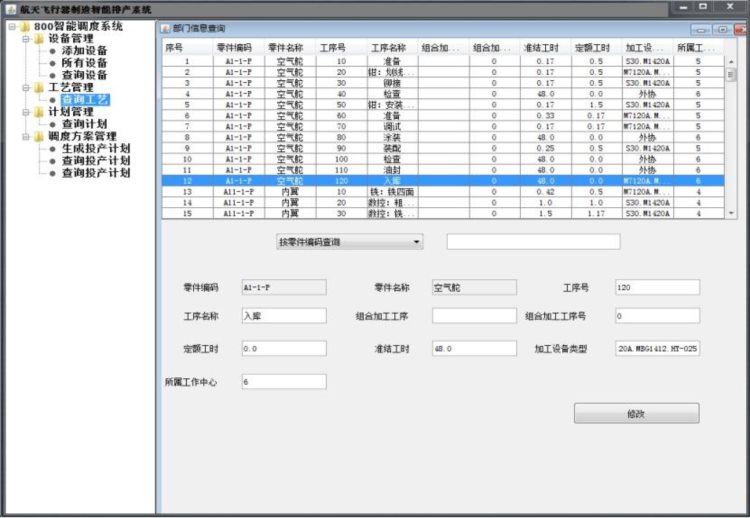
柔性生产线:加工过程自适应控制提升产线动态重构能力
航天离散制造智能工厂在已有机群、数字化生产单元等制造装备基础上,通过产线工艺集约化成组设计、柔性装夹子系统、线内物流配送子系统、标识与综控子系统的有效衔接与集成,构建了舱体自动化柔性生产线,满足生产计划和设备资源等快速变化工况下的自适应混线高质量高效率生产。
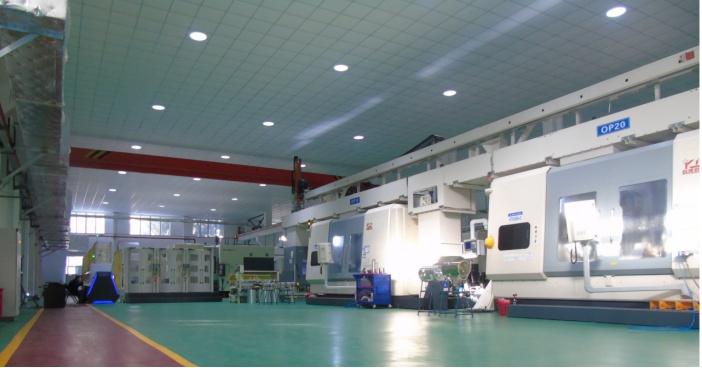
智能在线检测:AI算法为产品质量保驾护航
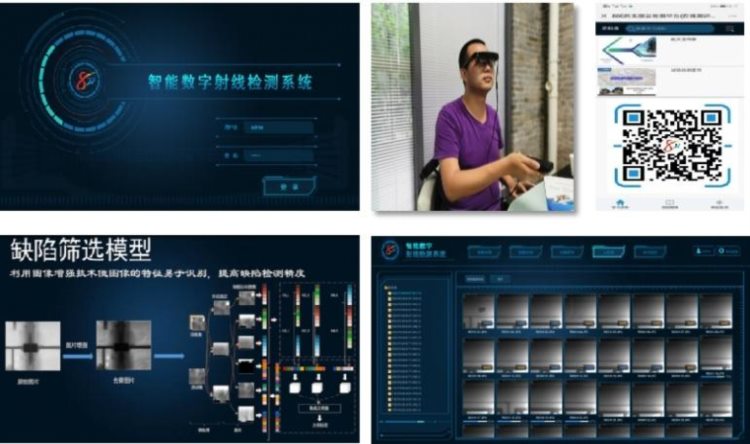
航天离散制造智能工厂应用机器人数字射线检测装备,融合焊缝缺陷机理、物性和成分分析,结合基于深度学习的图像分类及缺陷位置检测算法以及HIS、IMG等格式图元数据读取和分析技术,开发了基于AI的智能云检测平台,实现了从焊缝X射线监测图像自动获取、图像在线预处理、焊缝缺陷智能评判、质量数据统计分析和全流程质量追溯等功能的智能化集成应用,实现精细化质量管控,降低不合格率,持续提升产品质量。
项目成效
航天离散制造智能工厂基于数据思维,围绕航天产品研制全周期数字主线,以数据的自由规则流动驱动业务实现产品、生产、业务三个维度的无缝集成,通过数字空间和虚拟空间的映射交互,实现车间智能管控和运行优化。
在整体赋能平台方面:按照分层和服务化的思想,基于微服务、中台、大数据等新一代IT技术和理念,融合航天工艺知识,构建面向航天离散制造行业的数字化转型基础设施,形成一系列微服务,涵盖七类34个微服务100多个业务功能,实现了科研生产、经营管理和供应链协同业务100%在线、过程100%透明、信息100%可追溯,生产过程人工统计工作减少80%以上。
在工艺数字化设计方面:通过零部件特征自动识别、加工区域构建、刀具智能决策与工艺路线智能优化,自动生成数控加工程序,减少航天产品工艺设计、准备需要的人力20人天/月;提高数控加工编程效率10倍以上。
在智能排产与调度方面:有效改变了传统航天产品生产人工调度排产、纸质信息反馈的模式,应用先进的嵌套分割算法实现车间智能排产与生产调度,达到了型号调度人员减少35%、车间智能排产单次优化响应时间<3min、生产任务平均生产周期缩短35.5%以及计划延误率下降25%等成效。
在生产柔性化方面:对标黑灯工厂,通过舱体柔性化生产线的打造,舱体综合生产节拍缩短到3h/件,数控机床设备有效利用率达到65%以上,一次交验合格率达到99.9%,满足4型8种舱体换线生产。
在智能在线检测方面:智能识别与人工判定相比,工作量提升95%的前提下,评片人员可以减少50%以上;应用工业互联网+AI的云检测模式,通过远程智能评片,比传统人工方式缩短98.3%。
航天离散制造智能工厂具有软件定义、数据驱动、智能生产、虚实融合四大特征,解决了基础赋能平台、智能工艺设计、智能排产调度、自动化生产等业务痛点10 余项,达到关键设备数控化率100%、设备综合利用率提升20%、生产效率提升30%等显著成效,实现了业务全在线,过程全透明,信息全追溯,大幅提升了数字化研制批产能力,走出了航天“老厂换新”的独特模式,在军工企业和离散制造行业具有较好的示范引领作用。
觉得不错请点赞!