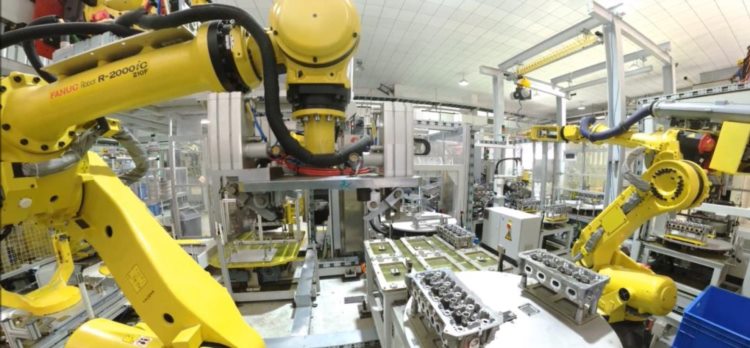
记者丨林安东
图片来源丨受访者提供
智能化不是简单地让机器帮人解决问题,而是一种思想上的转变。这家智能工厂用“客户直连”+“柔性智造”这套组合拳满足了客户日益个性化的需求。
在上海新动力汽车科技股份有限公司(以下简称“动力新科”)的D20智能工厂内,工业机器人、AGV小车在不停地工作,生产管理人员通过现场大屏、电脑和手机能实时掌握生产运行状态。
“为客户带来更高品质、更高一致性的产品,更短的产品交付周期,并满足客户日益增长的个性化定制需求,是这个工厂诞生的初衷。”动力新科制造部副部长宋佳峰说。
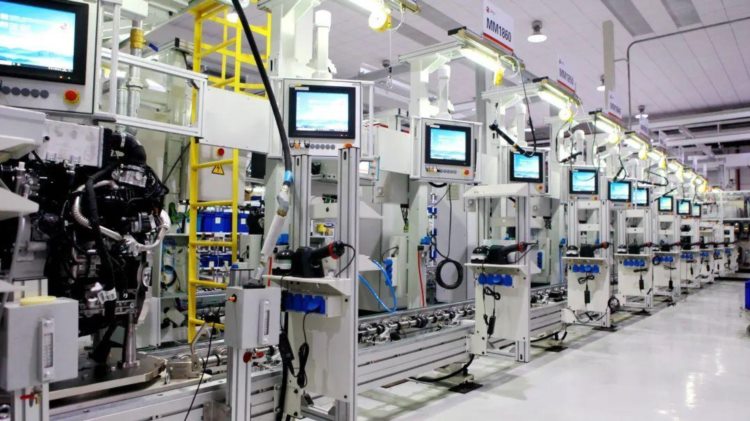
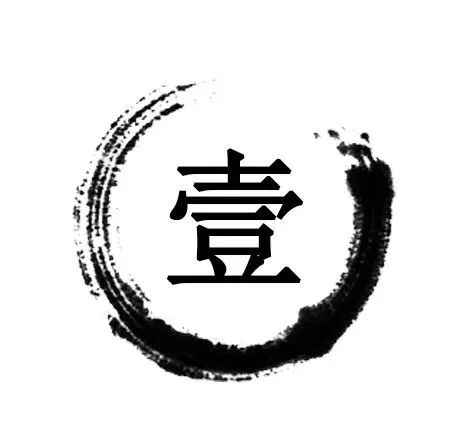
一条产线生产200多种产品
“2.0T高性能商用车柴油发动机是公司当前重要的拳头产品。目前广泛应用于上汽大通的六个平台上,也吸引了业内外客户的关注。”宋佳峰说,“就这一款发动机,机型的变化已经超过了200种。”
面对“多品种,小批量”的订单特点,动力新科在D20智能工厂首次采用自主开发的APS高级排程系统。“这套系统实现了与整车厂的订单信息互通。当整车的订单顺序一生成,APS系统就会基于既定的约束条件进行智能排产,在确保满足订单交付的同时实现最精益的排产,从而有效降低了整机库存,又有效缩短了交付OTD(一台发动机从主机厂发订单到这台发动机交付的时间)。”宋佳峰说。
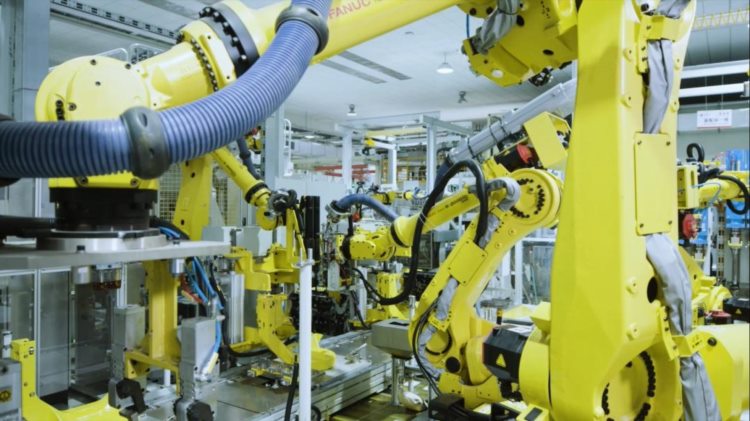
当然,要在一条产线上生产出200多种不同的产品,光靠一套排产系统还不够。“因为产品的种类非常多,我们很难通过标准化的指导文件去培训生产线上的员工。为此,我们专门采用一套名为APM(装配工艺管理)的系统。”宋佳峰表示。
有了APM这套系统,当一台发动机到达一个工位,都会有对应的信号传输到系统,系统会根据这个信号把这个机型对应的物料清单(BOM)调用出来,装配线员工要在这个机器上装哪几个零件、零件号是多少、数量是多少都一目了然。
据了解,通过全供应链过程管理,优化供应链端到端全过程的业务效率,APS+APM的组合拳显著提高了D20工厂的产能与资源利用率。原本OTD是108小时,如今已经缩短到了36小时。“如果没有这些智能系统做支撑,这200多种发动机产品想要充分满足整车厂客户的个性化需求,对整个供应链的资源协调来说需要庞大的工作量,零部件和成品的备库还需要海量的成本。”宋佳峰说。
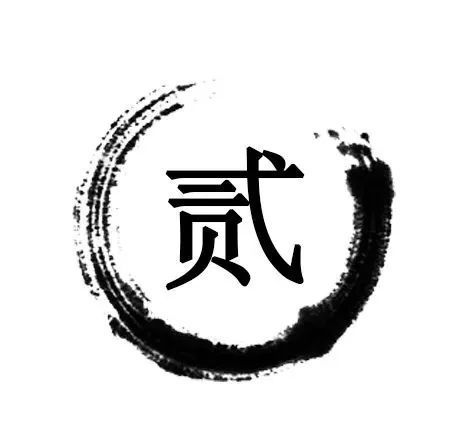
业务数据化解决更多问题
“我们还开发了一套业务数据化管理系统,实现了生产制造全过程在线管理。”宋佳峰打开电脑,为记者展示了数据化看板界面。这套系统真正做到了“一单到底”,每一台发动机上线、下线、试车、报交的每一个阶段情况都能实时监控。任何一台发动的生产节奏出现异常,系统就会以问题清单的形式进行预警提示。
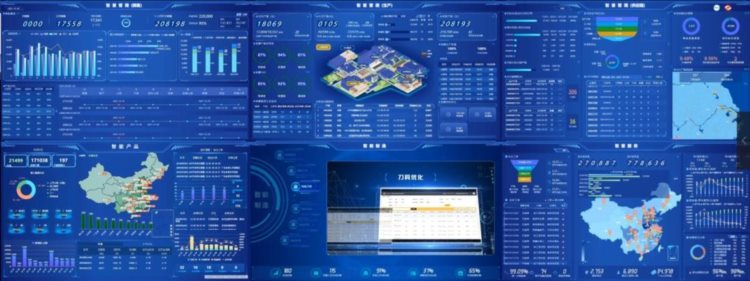
“另外,通过业务数据化之后,很多原来不是问题的问题,都会通过数据暴露出来。”宋佳峰说,“通过实时的数据监控,停机5分钟、10分钟这些没有影响到整线生产目标的小问题也会被及时地发现,大胆地暴露问题对我们快速解决问题、预先采取措施避免问题提出了更苛刻的管理要求。这两年里,设备的损工下降了86%,15分钟以上的停线次数下降了43%。”
在前不久,D20智能工厂的MES(制造执行管理系统)系统每天都会出现全天累计不到10分钟左右的系统卡滞,这一异常表现也被记录了下来。经排查,IT部门发现由于长时间满负荷运行之后,系统的内存占用满了,于是IT部门提高了计划性清空内存的频率。
“我们不能小看这10分钟,如果是300天那就是3000分钟,全年下来造成的产能损失不容忽视。”宋佳峰说,“正因为业务数据化之后,我们分析问题的颗粒度越来越细,这些高频、低损耗的问题能够更及时被发现和解决,真正让我们做到了消除浪费,不断改进。”
如今,在动力新科的各个车间里,都能看到实时统计的数据大屏。D20智能工厂就像动力新科的桥头堡,把运用成熟的智能制造技术和方法不断辐射到其他车间去。
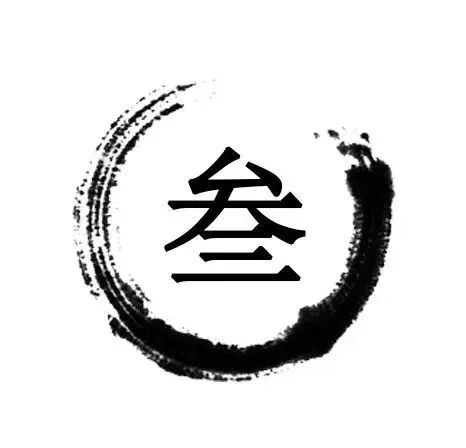
智能化全面生根发芽
为了进一步提升工厂的智能化程度,D20智能工厂还规模化地引入视觉防错系统和在线自动测量技术,实现了部分以往需要人工干预的防错、质检岗位的自动化,提高了流水线防错能力和质量风险管控预警能力。
“比如涂胶类的工作,我们现在基本上都是靠机器人自动涂胶,涂完胶之后,视觉防错系统就会比对胶线位置是否符合标准。如果不符合标准,系统就会报警提示员工返工。”宋佳峰说,“通过这些技术的运用,在质量管理方面和生产效率都有明显的提升。”
不过,动力新科的智能化发展不仅仅体现在硬件和软件上。随着智能化在动力新科车间内的应用逐渐增加,“智能化”的思维开始在一线员工中“生根发芽”。
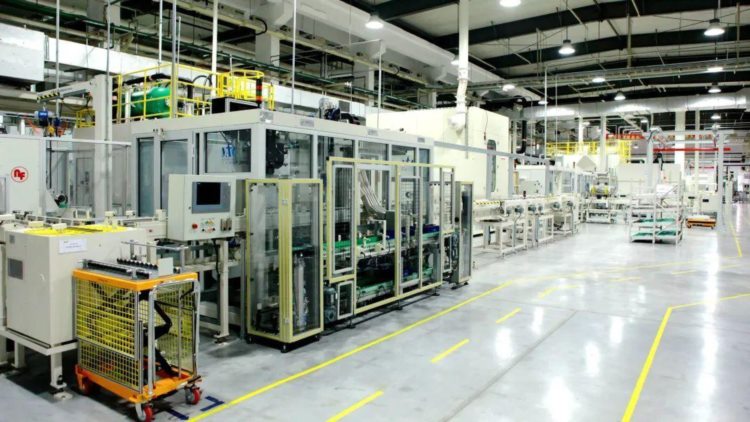
“就比如说缸盖机加工有一个涂胶防错验证的工艺要求,需要员工每天开班的时候钻进机床去验证涂胶质量,他在装配线轮岗以后,根据装配线的涂胶视觉防错系统,在他原来的机加工岗位上提出合理化建议装上了视觉识别的功能,既提高了验证质量又规避了进出机床的安全风险。又比如说,装配线上有一些工具有使用寿命的要求,之前通过手动方式记录使用次数。现在员工借鉴机加工刀具寿命统计功能,在MES中增加一个倒计数小程序,用几乎零成本的小改进就从根本上解决了问题。现在我们的员工经常会在合理化建议中提出这种用新技术、新程序、新功能解决实际问题的案例。”宋佳峰说,“员工在智能化方面的意识和想法变多了,我觉得这是动力新科这些年来智能化发展的另外一个比较宝贵的收获。”宋佳峰说。