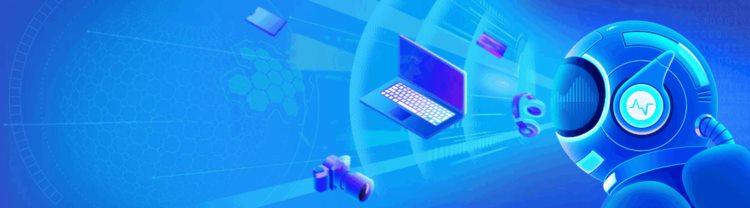
节能先进
在市经济信息化委指导下,市节能中心自2012年开展单位产品能耗限额标准专项检查以来,经过多年贯标培训和节能监察,有力推进企业节能管理水平提高、能效水平显著提升,助力高效、清洁、低碳、循环的绿色产业体系的形成。“十四五”是实现碳达峰目标的关键期和窗口期,需要工业和通信业绿色发展持续发力,为进一步加强节能监察工作,建立常态化节能监察机制,突出抓好重点领域、重点单位、重点项目的监督管理,按照国家和本市2022年度节能监察工作任务,市节能中心开展了2022年度单位产品能耗限额标准专项检查工作,挖掘出一批在能效水平和节能管理方面具有代表性、引领性、先进性的单位。我们将专题分享2022年度工业和通信业达到行业先进水平的单位案例,促进全市相关领域企业加强交流互鉴,推进节能降碳,加快节能新工艺、新技术的应用,推动全行业“比、学、赶、超”行业先进者的经验方法,提升产业绿色低碳化水平。
企业基本情况
延锋彼欧汽车外饰系统有限公司(以下简称“延锋彼欧”)成立于2007年4月,总部和技术中心位于上海嘉定,其前身为延锋伟世通外饰厂,公司在原有安亭、重庆两个生产基地的基础上,通过持续努力,发展成为国内领先的汽车外饰系统供应商。截至2022年底,公司拥有30个工厂实体,保险杠销售占比位居中国市场第一。延锋彼欧(上海)汽车外饰系统有限公司在2020年荣获上海市能效“领跑者”(第三批)—铜牌能效“领跑者”称号。
案例简介
延锋彼欧将始终致力于可持续发展,履行企业社会责任。在双碳目标的大背景下,为满足企业长久发展,与全球重要客户达成碳中和远景,延锋彼欧启动公司可持续发展碳中和的路径规划。成立可持续发展委员会,该委员会成员包括公司执委会成员、经营委员会成员。可持续发展委员会设立了双碳目标并推进包括绿色低碳在内的各相关可持续发展工作。
企业节能实践
案例1:工艺技术改造
汽车外饰的生产工艺特性,其生产模式属于“高能耗”和“高成本”。自“十二五”以来,公司持续不断投入和推进各项重大设备节能技改和减排措施:在注塑方面,改造注塑机伺服动力、注塑机二板化与电动化、节拍周期同步化、全自动变频供料系统等;在喷涂方面,涂装线循环风系统、蓄热式热氧化炉RTO设备应用、多项高温烟气热回收应用、冰水机系统模糊控制;在公用动力方面,空压机变频及自控系统、全工厂LED照明、储能系统等。同时,环保的水性涂装线、干式喷房、全电动输调漆系统等,在新基地建设和新设备规划广泛应用,企业自始坚持将更节能环保的技术作为公司内标准推广复制。

行业首个旧涂装线改造应用干式喷房
案例2:数字化能源管理
延锋彼欧通过引入能源管理体系制度以及数字化来助推节能低碳。2016年,根据能源管理体系的要求和管理方法,公司彻底梳理并制定了一整套符合能源管理体系要求、适合延锋彼欧更有效落实能源管理制度的文件体系。深入地从能源计量、能源监控,到绩效控制、持续改进建立了系统化、规范化的文件制度,全面提升了公司节能管理的体系基础。通过系统性的改制过程,管理团队在企业推进能源评审工作,引导节能管理向体系建设思路转变。通过体系导入,公司明确了各管理人员、部门科室、生产单元等在节能管理中应尽的职责,规范了原先运营环节中多种不合理场景,打通了持续挖掘和提升节能成效的必经之路。在2017年通过上海市重点用能单位能源管理体系建设效果的符合性评价。
2018年起,在能源管理体系的指导框架下,延锋彼欧积极探索通过数字化能源管理信息系统进一步提升公司节能降碳的可持续性。能源管理信息系统,历经3年的规划、部署、实施和应用,项目团队完全自主开发了多种贴合企业实际痛点的诊断工具和案例。延锋彼欧能源信息系统以能源管理体系为准绳,覆盖“操作级、管理级、决策级”三层次能源管理架构:全电子化能源数据采集、符合能源计量制度的硬件网络标准化;自动生成常规能源分析图表、基地能源消费可视化,形成多维度数据分析和异常报警;重点生产设备和动力设施能效实时监控全覆盖,并做到与生产数据有效结合,更贴近生产实际;针对痛点场景而开发的专属功能,如涂装开关机管理、空压机自动联动、电力MD监控算法等。所有这些通过信息化实现的改进,解决了以往公司节能工作过程中低效、粗放的管理模式,充分体现了信息化赋能“精益生产”。

延锋彼欧数字化工厂成果
案例3:加强绿色能源利用
在2015年,延锋彼欧安亭工厂就成为延锋集团内首批投建分布式光伏电站的基地。通过合同能源管理的模式,既降低了项目门槛,同时最大化了公司绿色收益。截至目前,延锋彼欧已有5座分布式光伏电站投入使用,年发电量规模达到4300MWh。同时,公司从2021年起,已经将分布式光伏电站定义为未来所有新建基地的标准配置。除此以外,上海总部积极协调和支持各外省市基地在当地的绿色电力获取,主动通过第三方售电模式来提高基地的可再生能源使用比例;主动通过购买中国绿证、国际绿证等减碳措施,来逐步实现工厂基地完全使用可再生电力。

延锋彼欧总部大楼分布式光伏电站
案例4:打造可循环材料体系
当前汽车行业对循环再生材料的呼声和需求越来越高,部分整车厂商OEM已将使用循环再生材料作为争取业务的敲门砖。延锋彼欧于2019年启动了循环再生材料发展规划,相继与国内主流材料供应商进行深度合作,通过密度、颜色、近红外等多种先进的筛选工序,严选出品质优异的回用基料;同时深入配方研发,对循环再生材料的机械性能、油漆适配性、产品成型工艺、CAE仿真分析、总成实验、碳排核算等进行研究,构建了循环再生材料回用比例与材料性能、减碳及成本的关系,最终开发出定制化外饰循环再生材料。至今,延锋彼欧已建立了适用于非功能性、非外观件及功能性、外观件的循环再生材料体系。与原生料相比,所开发的循环再生材料的机械性能保持在85%以上,实现减碳20%-50%,并有望今年初开始量产应用。在绿色材料方面,除了循环再生材料,延锋彼欧针对生物基、化学循环材料也在同步开展研究,有望在2030年前投入应用。
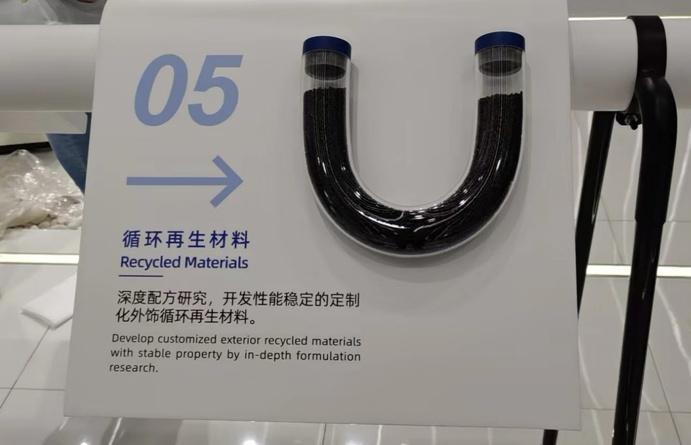
定制化外饰循环再生材料
企业未来在节能上的打算
延锋彼欧将坚持探索,不断突破,打造“延锋特色”的绿色低碳行动路径,为汽车零部件企业的低碳未来贡献“延锋方案”和“延锋力量”。目前公司已拟定“十四五”期间的减碳目标。预计到2025年末,可再生电力使用占比达到20%以上;继续推进分布式光伏电站建设,力求达到12500MWh/年的发电规模;水性涂装线作为设备建设标准,达到8条以上;为有需求的客户实现25%的循环再生材料应用。